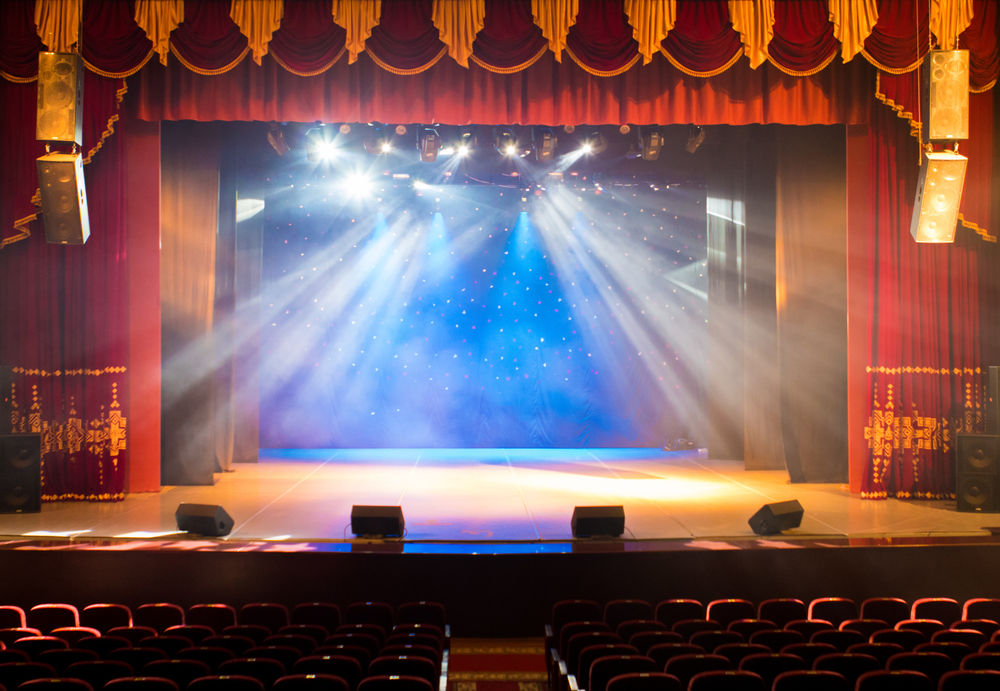
Production Process
Lighting Prep for Alice
Before the creation of the actual production could begin, our job as lighting technicians was to unpack all the fixtures and test them to make sure they were not damaged and working to their full capabilities. We did not do this at the old rep but at BOA instead. Any fixture that was damaged was labelled with red tape that had writing on stating the problem and was sent back tot the provider (PRG) so that it could be replaced with a working fixture (that was also tested). After we were sure al the required fixtures were working, we re-packed them into their flight cases and placed custom made Alice stickers on the cases with the contents of the flight cases being written onto each sticker so that there is no confusion on which fixtures are in which case when unpacking them at The Old Rep.


Load Out
After the Lighting prep, we had to transport all of the lighting fixtures to the old rep. This meant we had to move each of the flight cases into a moving van (hired out by boa) so that they could be transported to The Old Rep. We individually loaded both set pieces and flight cases into the back of the van till it was full, where the parts were transported and unloaded at the old rep before returning to BOA. This repeated multiple times until all set and cases were transported to The Old Rep.
Get In and Rigging
We were slightly behind schedule when we first got in, it took the set construction team longer originally planned to get the big pieces of the set up on stage; So, for the first half of the first get in day we were assisting in setting up the large pieces of the set. After the large and space consuming pieces were up, we could finally start setting up some of the LX. Originally, he had a rig plan where we were split into groups, each group setting up one bar of LX; however this plan was thrown out the window as some set pieces where still being put together, so we all worked on what bars were available and finished the last 2 the next day. The second day of Get In, we set up the fixtures on the two perches and the side bars. We addressed all the fixtures and they were patched into the EOS desk we were using, we tested them to double check they still worked and were not damaged during transportation.


In terms of power, we were spread very thin powering all the Lx fixtures (including the very expensive projector). we used quite a few 16amp splitters to power most of the fixtures and on Lx4 and Lx5 all 13amp plug sockets were almost all used up. This meant that if the lighting designer wanted more fixtures up, then the power may not be able to power all fixtures and we could end up tripping a breaker switch in the middle of a show, or a lamp could stop working or a bulb could blow causing many safety risks to all in the building.

Due to the already overflowing abundance of cables and lack of lengthy cables, we daisy-chained DMX cables between fixtures to try and keep cable management as effective as possible and not have more cable than bar. Daisey Chaining is effective because it limits the amount of lengthy cables needed meaning you can use the shorter cables (like 3m and 5m) meaning cable management is not as tricky to deal with and doesn't make the bar look like it is one massive cable itself.
After successfully cabling the fixtures, we patched them into a Eos desk that the year 13s had set up on a makeshift desk in the center of the auditorium. Considering we had so many fixtures on each bar, patching them took a while to complete. I didn't do most of the patching at the desk, but rather stood on stage and read out some of the addresses while simultaneously helping set up the fixtures on perch stage left. getting the fixtures up to the perches was not too tricky considering the fixtures we were moving were very light. I would stand at the bottom of the ladder and lift myself up as far as I could go with one hand and use the other to hand the fixture to someone on the perch; they would rig the fixture and I would read out the patch number labelled on the rig plan we had created. I relayed back to the desk that the perch fixtures were ready to be soft patched into the desk. Overall the perches were not much effort and we had them ready to be soft patched in about 30-45 minutes.
Cue recording and Desk operation
One of the year 13s had already created a whole collection of pallets on the EOS desk; one was an overview of the theatre and all its fixtures, there you could manually select fixtures to control them individually or groups if you selected multiple at once. There was also a groups pallet where all fixtures were sorted into groups such as intelligent lanterns, perch fixtures, side bars, LX bar groups (LX1 LX2 LX3 LX4 LX5). These pallets were nothing fancy but their purpose was to make fixtures accessible by tapping the screen once instead of having to find the fixture on the address page, which was time consuming and frustrating considering there was so many fixtures. Considering everyone had gone on lunch and i was already back. One if the year 13s gave me a quick tour around the pallets and asked me to create cues for his new stage position pallet. I individually moved each intelligent fixture to Centre stage and pressed the update button to update the empty cue, I did this for CS, CSL, DSL, DSR.
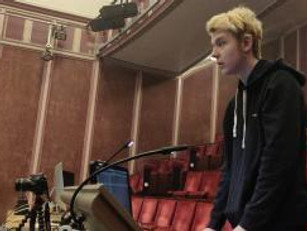
After everything all LX, sound and set was up and running, it was time for tech rehearsals and dress rehearsals. This meant someone needed to work the lighting desk cues. Desk operation is pretty simple. You have a list of cues on a monitor, and you have a go and back button. to move to the next cue press go and press back to stop the transition and press again to go back. There will be a SM that will have a cue list for all of the crew (including LX, Flys, Spots, Sound and Visual).
Each group is connected via a headset radio system that we call CAMS, The DSM will call a specific group(s) and ask for them to be on standby, stating which cue to be waiting for, then say go meaning press the go button. For example, the DSM will say "LX cue 38 on standby" you reply "LX standing by", they tell you when to go and you hit go. There are also visual cues (which are labelled on the cues list) where you have to visually see an event happen and judge when to go yourself as the DSM will not call the cue. I operated two dress rehearsals and two actual shows both going pretty smoothly, the visual cues were a little difficult to do but after one or two attempts I believe I called the cues pretty well.
Floating Tech and interrelation with Stage Management
Floating tech, means you are an extra set of hands for any technical aspects of the show that cannot be controlled from the desk. For our production, this included a haze machine in the pit that was to be used at the end of the opening song at the start of the show. The white rabbit sits on the edge of the stage and jumps down. You, the floating tech, will be in the pit (an area under the stage) controlling a haze machine with a remote. The desk operator will turn on some pink gelled parkans in the pit which is your cue to fire the machine filling the pit with smoke as the white rabbit enters through the pit. After this, you switch off and unplug the smoke machine and wait until the tear drop scene, you hand a blue tarp that is already in the pit, through the small gap in the pit door to the actresses playing Alice's children. After that, you must take the smoke machine up the red spiral staircase and place it behind portal 1, power it up and get ready to fire it for the caterpillar entrance scene.
After the caterpillar entrance, floating techs job is basically done, from there you can help out stage management with prop management and with the large ramp used in the mad hatters tea party scene, before and after the "One place round" song.
The Production of Alice ran smoothly with little to no hiccups, all viewings of the show ran incredibly well. I was pleased with my input on the show, I felt as if I was a help doing the get in and get out where I rigged up fixtures onto bars and ensured they were correctly powered and dmx'd while also making sure I was conforming to the health and safety guidelines with my hard hat and steel toe capped boots. I also felt that my desk operation during the shows was great. However, I also could have helped others in setting up their bars during the get in and should have been more precise on the cue lab as some of my cues were too sloppy and did not match well with the beat of the song. I could have developed these skills further by learning to create cues as well this would have developed my skill set even more allowing me to understand the process from start to finish. I feel I have learnt and developed new skills such as rigging and powering with the correct cables using the correct amount of amps; operating the desk by programming placement of fixtures and using the cue list during shows. Sometimes during the shows of Alice when I was operating the cue lab on Alice, the DSM would call cues late, this meant I had to use my own initiative and activate the next cue based off of my own call.
​